Extreme Cold Warning in the United States: The Science Behind the Deep Freeze
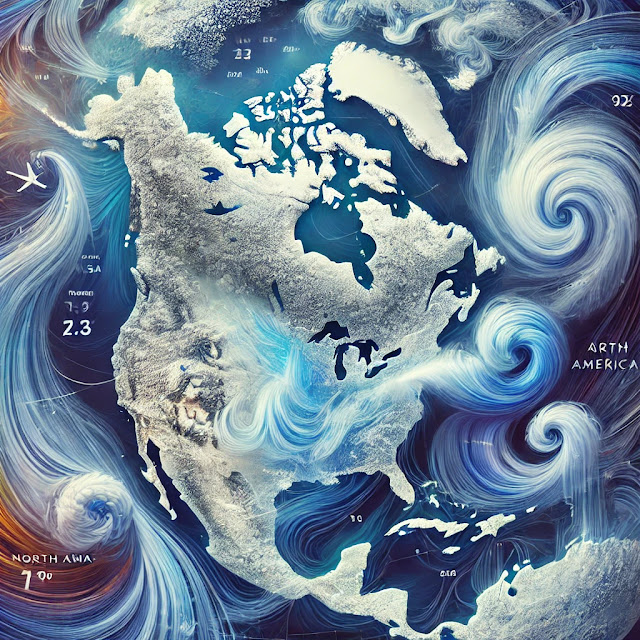
Extreme Cold Warning in the United States: The Science Behind the Deep Freeze Introduction As temperatures plummet across the United States, extreme cold warnings have gripped large portions of the country. The bone-chilling cold isn't just inconvenient—it's dangerous, affecting millions of lives and disrupting daily activities. But what causes such extreme cold spells, and how does science explain these phenomena? Let’s delve into the meteorological and scientific reasons behind these frigid temperatures. What is an Extreme Cold Warning? An extreme cold warning is issued when temperatures or wind chill values are so low that they pose a risk to public safety. Frostbite, hypothermia, and other cold-related illnesses become real threats in these conditions. The thresholds for such warnings vary depending on the region but are typically issued when the wind chill drops to dangerous levels. The Science Behind the Arctic Chill Polar Vortex The primary driver of extreme cold in the...